ELECTROLESS NICKEL PLATING SERVICES
The higest quailty EN plating for telecommunications and other critical applications
Electroless nickel plating (also known as EN) is extremely reliable as well as versatile due to its ability to deliver even plating thicknesses that allow for tolerances to be achieved. Additionally, electroless nickel plating services offers some of the best corrosion protection available.
Mid Atlantic Finishing Corp. offers electroless nickel plating services to a variety of industries Nationwide including telecommunications, aerospace, defense, medical and RF + microwave sectors.
ELECTROLESS NICKEL PLATING TO THE FOLLOWING SPECIFICATIONS:
MAF’S nickel plating services adhere to most Telecommunications specifications.
MIL-C -26074
CLASS 1: As plated no subsequent heat treatment (a bake for hydrogen embrittlement relief is not considered heat treatment).
CLASS 2: Heat-treated to obtain required hardness. May be used on all metals not affected by heating to 500F and above. Required hardness can be obtained per the following schedule:
°F TEMP | HOURS |
500 | 4 or more |
550 | 2 or more |
650 | 1.0 to 1.5 |
720 | 0.5 to 1.0 |
CLASS 3: Aluminum alloys non heat-treatable, and beryllium alloys processed to improve adhesion of the nickel deposit.
Coated non-heat aluminum parts shall be heated for 1 to 1.5 hours at 375°F +/- 15°F to improve adhesion of nickel deposit.
CLASS 4: Aluminum alloys, heat-treatable, processed to improve adhesion of the nickel deposit.
Coated heat-treatable aluminum alloys shall be heated between 240°F to 260°F for 1 to 1.5 hours to improve adhesion of nickel deposit.
GRADE A: 0.0010-inch minimum deposit thickness
GRADE B: 0.0005-inch minimum deposit thickness
GRADE C: 0.0015-inch minimum deposit thickness
ASTM B733
NOTE: ASTM B733 is markedly updated from ASTM B733-90 in that the coating Type specifies the phosphorous content of the coating. ASTM B733-90 does not make this distinction.
Type I: No requirement of phosphorous
Type II: 1-3% phosphorous (low phosphorous)
Type III: 2-4% phosphorous (low phosphorous)
Type IV: 5-9% phosphorous (medium phosphorous)
Type V: 10% or greater phosphorous (high phosphorous)
SC0: Minimum Thickness 0.000004 in
SC1: Light Service 0.0002 in minimum
SC2: Mild Service 0.0005 in minimum
SC3: Moderate Service 0.001 in minimum
SC4: Severe Service 0.003 in minimum
CLASS 1: As-deposited, no heat treatment.
CLASS 2: Heat treatment at 260 to 400°C (500-752°F) to produce a minimum hardness of 850 HK100.
CLASS 3: Heat treatment at 180 to 200°C (356-392°F) for 2 to 4-hr to improve coating adhesion on steel and to provide for hydrogen embrittlement relief.
CLASS 4: Heat treatment at 120 to 130°C (248-266°F) for at least 1-hr to increase adhesion of heat-treatable (age-hardened) aluminum alloys (such as 7075) and carburized steel.
CLASS 5: Heat treatment at 140 to 150°C (284-302°F) for at least 1-hr to improve coating adhesion for aluminum, non age-hardened aluminum alloys, copper, copper alloys and beryllium.
CLASS 6: Heat treatment at 300 to 320°C (572-608°F) for at least 1-hr to improve coating adhesion for titanium alloys.
AMS 2404
NOTE: AMS 2404 supersedes AMS-MIL-C-26074 which employs Grade designations to convey thickness requirements. See 8.13 for a complete cross reference from AMS-MIL-C-26074 callouts to the technically identical provisions within this specification (AMS 2404) in order to comply with the purchase order requirements.
CLASS 1: Except for hydrogen embrittlement relief, no post plating thermal treatment.
CLASS 2: Thermal treatment at 450°F (232°C) or above to harden the deposit.
CLASS 3: Thermal treatment at 375°F (191°C) to improve adhesion for non-heat treatable aluminum alloys and beryllium alloys.
CLASS 4: Thermal treatment at 250°F (121°C) to improve adhesion for heat-treatable aluminum alloys.
Unless a specific class is specified, Class 1 shall be supplied.
Stress Relief Treatment: Steel parts having a hardness of 40 HRC or higher and which have been ground after heat treatment shall be cleaned to remove surface contamination and suitable stress relieved before preparation for plating. Unless otherwise specified, the stress relief temperature shall not be less than 275°F (135°C) for not less than five hours for parts having hardness of 55 HRC or higher or not less than 375°F (191°C) for not less than four hours for other parts.
When Class 2 is specified, parts shall be heated to a selected temperature within the range of 450 to 800F and held for sufficient time to increase hardness of the deposit. See 3.4.4 and 8.6. Hydrogen embrittlement relief (3.3.1) may be omitted if Class 2 hardening is accomplished within four hours after plating.
When Class 3 is specified, parts shall be heated to 375°F +/- 15°F for 1 to 1.5 Hours.
When Class 4 is specified, parts shall be heated to 250°F +/- 10°F for 1 to 1.5 Hours.
Thickness: Unless otherwise specified, minimum thickness of the nickel coating shall be 0.0010 inch for aluminum based alloys, 0.0005 inch for copper, nickel, cobalt, titanium and beryllium alloys and 0.0015 inch for iron-based alloys.
Hardness: Class 2 plating shall be not lower than 800 HK100, or equivalent determined in accordance with ASTM E384.
Composition: The cognizant engineering organization may specify a phosphorus content range of the deposit. When specified, the composition of the deposit shall be determined by a method acceptable to the cognizant engineering organization.
The following thermal treatments have been used to achieve Class 2 hardness:
°F TEMP | HOURS |
450 | 4 hrs minimum |
500 | 4 hrs minimum |
550 | 2 hrs minimum |
650 | 1.0 to 1.5 hrs minimum |
750 | 0.5 to 1.0. hrs* |
Proactive Personalized Service
Prompt Quotes. Fast Turnaround Times
Suberb Qualilty, Value-Added Results
Competitive Pricing
PERFORMANCE BENEFITS
ITEMS OF NOTE
Electroless Nickel (high phosphorous or medium phosphorous as required) is similar to stainless steel in color.
Electroless nickel is used extensively in the salvage of worn or mis-machined parts. It is also widely used for inside dimensions and irregular shapes where assembly tolerances need uniformity that electroless nickel plating process provides.
PRECISION METAL PLATING TO EXACT SPECIFICATIONS
MAF Corp. is NADCAP approved for chemical processing by PRI International.
REQUEST A QUOTE
Precision metal plating services for aerospace, defense, medical and RF & Microwave sectors.
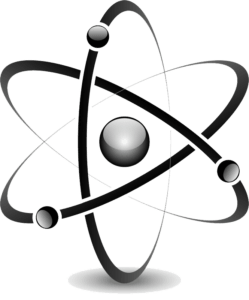